Technical Pathways and Practices for Enhancing Industrial Lens Performance
As a core component of machine vision systems, the performance of
FA industrial lenses directly impacts the accuracy and efficiency of the entire system. With the rapid development of smart manufacturing and Industry 4.0, the performance requirements for industrial lenses are continuously increasing. From optical design to material selection, from manufacturing processes to system integration, improving the performance of industrial lenses requires multifaceted technological innovation and optimization. Through systematic technical improvements and engineering practices, the performance of industrial lenses is achieving a qualitative leap.
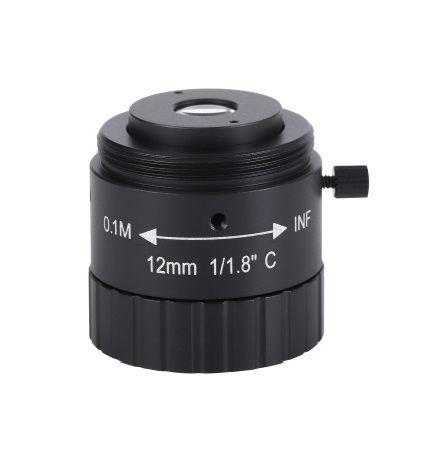
1. Optical Design Optimization
The use of advanced optical design software is the foundation for enhancing industrial lens performance. Modern optical design software such as Zemax and Code V enables the simulation and optimization of complex optical systems. Through the design of aspherical lenses and freeform surfaces, lens distortion is controlled below 0.01%, and resolution is increased to over 50 megapixels.
The application of multispectral imaging technology expands the application scope of industrial lenses. Through special optical coatings and filter designs, industrial lenses can achieve multispectral imaging in ultraviolet, visible, and infrared light. In a semiconductor inspection application, the use of multispectral industrial lenses increased defect detection rates by 30%.
Integrated optical system design is another important direction. By integrating the lighting system with the lens, system stability and usability are improved. In an automated inspection system, integrated design reduced system debugging time by 50%.
2. Material and Manufacturing Process Innovation
The application of new optical materials significantly enhances lens performance. The use of high-refractive-index, low-dispersion glass reduces chromatic aberration and astigmatism by 60%. Nano-level optical coating technology increases lens transmittance to over 99.9%.
Advances in precision machining technology improve lens manufacturing accuracy. Using ultra-precision CNC machining and ion beam polishing, lens surface accuracy reaches the nanometer level. In a high-precision industrial lens, this machining technology improved the MTF value by 20%.
The application of automated assembly technology enhances lens consistency and reliability. Through robotic automated assembly and online inspection, lens assembly accuracy is controlled within 0.1 microns. In a mass production scenario, automated assembly increased product yield from 95% to 99.5%.
3. Integration of Intelligent Functions
The integration of autofocus and zoom functions improves lens adaptability. Using voice coil motors and piezoelectric ceramic drive technology, millisecond-level focusing and zooming are achieved. In a rapid inspection system, intelligent autofocus increased inspection efficiency by 40%.
The application of image stabilization technology improves dynamic imaging quality. By combining optical and electronic stabilization, dynamic imaging blur is reduced by 80%. In a moving target detection application, this technology increased detection accuracy by 25%.
The integration of intelligent diagnostics and maintenance functions enhances system reliability. Through built-in sensors and self-diagnostic algorithms, lens condition monitoring and fault prediction are achieved. In an industrial setting, this functionality reduced equipment maintenance costs by 30%.
4. System Integration and Optimization
Collaborative optimization with image sensors is key to improving system performance. By matching optical design with sensor characteristics, the system's signal-to-noise ratio is improved by 40%. In a high-sensitivity detection application, this optimization lowered the detection limit by one order of magnitude.
Thermal stability design of optical systems enhances environmental adaptability. Using low thermal expansion coefficient materials and active temperature control technology, temperature drift is controlled within 0.01%/°C. In an outdoor application, this design kept system performance fluctuations below 1% under all-weather conditions.
Deep integration with artificial intelligence algorithms is the future development direction. By embedding deep learning algorithms into lens systems, intelligent image processing and analysis are achieved. In a complex defect detection application, this integration improved detection accuracy by 35%.
Enhancing industrial lens performance is a systematic project that requires innovation and optimization in optical design, material processes, intelligent functions, and system integration. With continuous technological advancements, the performance of industrial lenses will achieve even greater breakthroughs, providing more powerful visual perception capabilities for smart manufacturing and Industry 4.0. In the future, industrial lenses will deeply integrate with new technologies such as artificial intelligence and 5G, ushering in a new era of
Cnomax machine vision.