How to choose the right industrial lens for your production line?
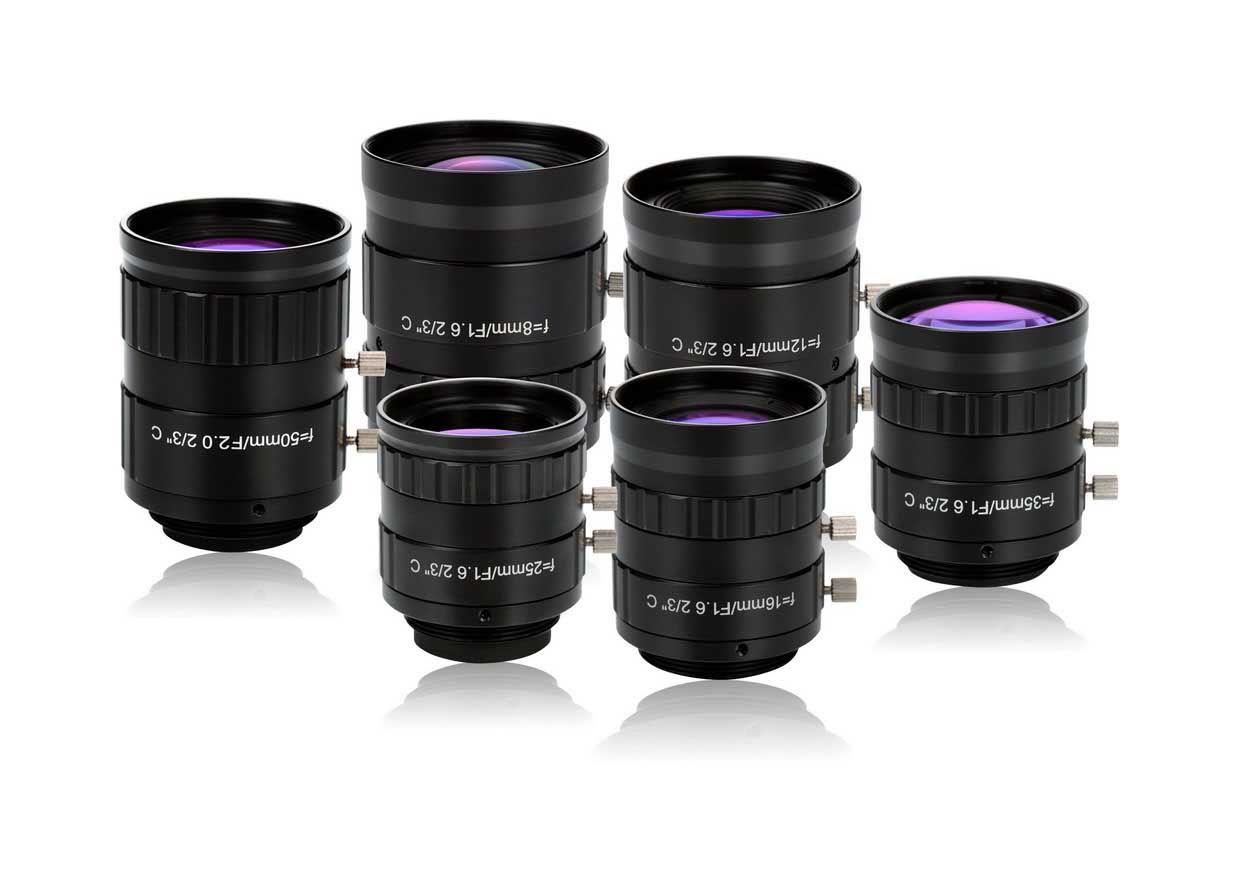
Selecting the right
industrial lens for your production line is a comprehensive process that requires considering the specific needs of the production line, environmental conditions, camera parameters, and the performance of the lens itself. The following is a detailed guide:
I. Clarify Application Requirements
1. Inspection Object: Understand the size, shape, material, and surface characteristics (such as reflectivity, transparency, etc.) of the target. These characteristics will directly affect the choice of the lens; for example, reflective surfaces may require anti-reflective lens coatings.
2. Working Distance: Determine the distance range between the lens and the object. This will influence the selection of focal length and depth of field.
3. Resolution Requirements: Determine the resolution required by the system based on the inspection accuracy needs. The resolution of the lens should match or exceed that of the camera to ensure image quality.
4. Environmental Conditions: Consider external factors such as temperature, humidity, vibration, and choose the appropriate protection level and material. For example, in high-temperature environments, lenses made of high-temperature-resistant materials are needed.
II. Understand Lens Parameters
1. Focal Length: The focal length determines the field of view and magnification of the lens. A shorter focal length provides a wider field of view; a longer focal length provides a narrower field of view. The focal length should be calculated based on the working distance and field of view requirements.
2. Aperture: The aperture size affects the brightness of the image and the depth of field. A large aperture is suitable for low-light environments but has a shallow depth of field; a small aperture is suitable for high-light environments and has a larger depth of field. The aperture should be chosen based on lighting conditions and inspection needs.
3. Field of View Angle: It refers to the maximum area that the lens can see, which is the effective working area that the lens can cover. The field of view angle is related to the focal length and working distance.
4. Depth of Field: It is the ability of the lens to maintain the required resolution when the object is closer to or farther away from the optimal focus point. The depth of field is related to the focal length, aperture, and working distance.
5. Resolution: The resolution of the lens, usually expressed in line pairs per millimeter (lp/mm), should meet or exceed the system's requirements for image detail.
6. Distortion: It refers to the deformation that may occur when the lens images an object, including barrel distortion and pincushion distortion. For high-precision measurement scenarios, lenses with low distortion should be chosen.
7. Interface Type: Ensure that the lens interface matches the camera interface, with common interfaces including C-mount, CS-mount, F-mount, etc.
8. Maximum Compatible CCD Size: It refers to the maximum clear imaging range that the lens can support, which should be greater than or equal to the size of the camera chip.
III. Choose Lens Type
1. Fixed Focal Length Lens: It has a fixed focal length, excellent optical performance, and is suitable for scenarios with fixed working distances and field of view angles. It is relatively low in cost.
2. Zoom Lens: It has an adjustable focal length, high flexibility, and is suitable for scenarios where flexible adjustment of the field of view angle or working distance is required. However, it is relatively high in cost.
3. Telecentric Lens: It is a specially designed lens that can eliminate parallax effects and ensure that the imaging size of the object does not change with its position. It is suitable for high-precision dimension measurement scenarios but is expensive.
4. Other Special Lenses: Such as macro lenses, ultraviolet lenses, infrared lenses, etc., should be chosen based on specific application scenarios.
IV. Consider Other Factors
1. Size and Weight: Consider the installation space and mechanical stability to avoid the lens being too large or heavy, which may affect the system operation.
2. Cost: Choose a cost-effective lens while meeting performance requirements.
3. Lead Time: Ensure that the lens lead time meets the project timeline requirements to avoid delays.
V. Testing and Verification
After the selection is complete, testing should be conducted in the actual environment:
1. Image Quality: Check the clarity, contrast, and distortion of the image.
2. Stability: Observe the performance of the lens during long-term operation.
3. Adjustment and Optimization: Adjust parameters or replace models based on test results.
VI. Case Study
Take the quality inspection on an electronic product production line as an example:
1. Inspection Object: Tiny electronic components, such as chips, resistors, etc.
2. Working Distance: Approximately 100mm.
3. Resolution Requirements: Able to clearly distinguish defects of 0.01mm.
4. Environmental Conditions: Normal temperature, normal humidity, no vibration.
Based on the above requirements, the following considerations can be made when choosing a lens:
1. Focal Length: Estimate the focal length using the formula f = WD × H / H_{sensor}, where WD is the working distance, H is the target height, and H_{sensor} is the sensor height. Assuming a sensor height of 8mm and a target height of 5mm, the focal length f = 100 × 5 / 8 = 62.5mm. A lens with a close focal length, such as 60mm or 65mm, can be chosen.
2. Aperture: Choose the aperture size based on lighting conditions and inspection speed. If the lighting is sufficient and the inspection speed is fast, a smaller aperture can be chosen to increase the depth of field.
3. Resolution: Choose a lens with a resolution higher than that of the camera, such as a lens with a line pairs per millimeter count greater than the camera sensor pixel density.
4. Lens Type: Since tiny defects need to be inspected and the working distance is fixed, a fixed focal length lens can be chosen. If high-precision measurement of component size or position is also required, a telecentric lens can be considered.
In summary, selecting the right industrial lens for a production line is a comprehensive process that requires considering multiple factors. By clarifying application requirements, understanding lens parameters, choosing the lens type, considering other factors, and conducting testing and verification, the accuracy and effectiveness of the selection can be ensured.