Industrial lens installation and debugging skills overview
As the core component of machine vision system, the installation and debugging quality of industrial lens directly affect the performance and use effect of the system. Proper installation and commissioning can not only give full play to the performance of industrial lenses, but also extend their service life and improve the stability and reliability of the system. From the preparation before installation to the parameter optimization in debugging, from the troubleshooting of common problems to the maintenance skills, this article will give you a detailed introduction to the installation and commissioning of
industrial lenses.
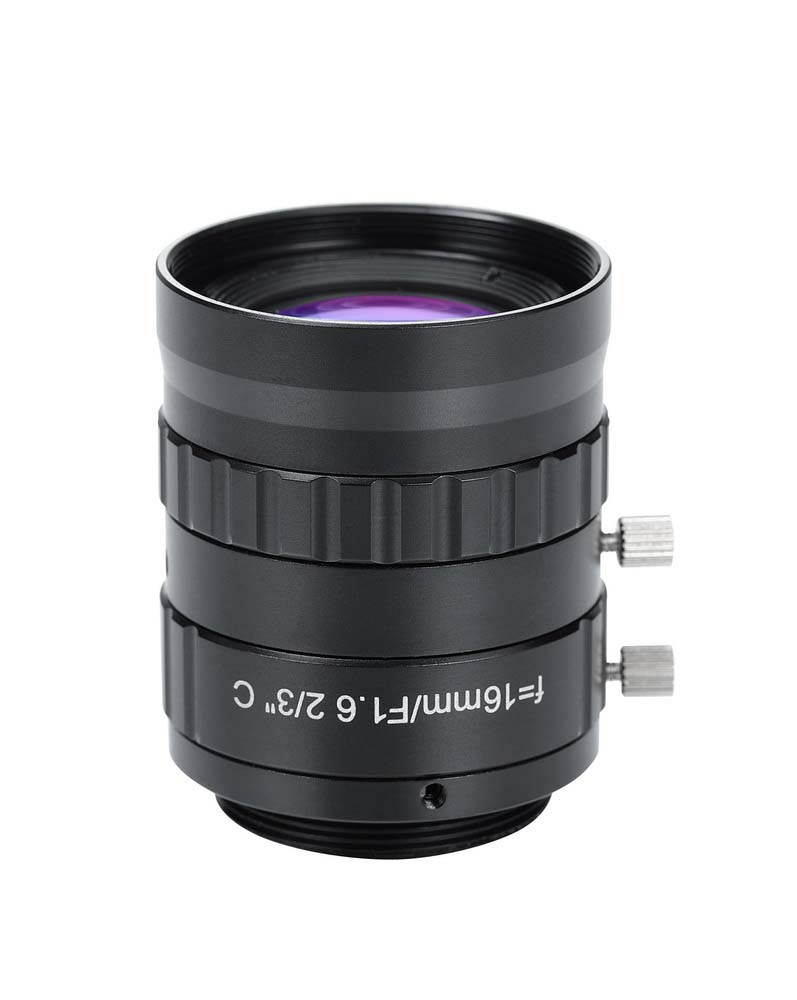
1. Preparation before installation
Environmental assessment is the first priority before installation. It is necessary to evaluate the temperature, humidity, vibration and other factors of the installation environment to ensure that the environmental conditions meet the working requirements of industrial lenses. In a semiconductor inspection project, image quality problems caused by temperature fluctuations were avoided by assessing environmental conditions in advance.
Equipment inspection is the key to ensure smooth installation. Check whether the packaging of industrial lenses is intact, whether there are scratches or stains on the surface of the lens, and whether the interface is matched. In an automatic production line, the installation failure caused by interface mismatch was avoided through strict equipment inspection.
Preparing tools is an important guarantee for installation. Special installation tools, such as a torque wrench, level, and cleaning tool, are available. In a precision measuring system, the installation accuracy and stability are ensured by using special tools.
Second, the installation process skills
The choice of installation position directly affects the image quality. Select the appropriate installation position according to the application requirements to ensure that the distance and Angle between the lens and the measured object meet the requirements. In a surface inspection system, the detection accuracy and efficiency are improved by optimizing the installation position.
The choice of the fixed method is the key in the installation process. It is necessary to choose the appropriate fixing method according to the weight and size of the industrial lens, such as bracket fixing, flange fixing, etc. In a high-speed detection system, the effect of vibration on the image quality is reduced by using a high rigidity bracket.
The handling of the connection interface is an important part of the installation process. Ensure that the interface is securely connected to avoid loose or poor contact. In an industrial inspection system, the reliability of the interface connection was improved by the use of locking screws and sealant.
3. Skills in the debugging process
Focal length adjustment is the primary task during debugging. You need to adjust the focal length of the lens to ensure that the image is clear. In a precision measuring system, the debugging efficiency and precision are improved by using the autofocus function.
Aperture adjustment is the key in the debugging process. The aperture size needs to be adjusted according to the lighting conditions and imaging needs to ensure that the imaging brightness and contrast are moderate. In a low illumination environment, the image quality is improved by optimizing the aperture adjustment.
Parameter optimization is an important step in debugging process. Lens parameters such as exposure time, gain, etc. need to be adjusted according to the needs of the application. In a high-speed motion detection system, the resolution and stability of the image are improved by optimizing the exposure time and gain.
4. Troubleshooting and solving common problems
Imaging blur is one of the common problems. Possible causes include misalignment of focal length, improper aperture setting, lens contamination, etc. It needs to be solved by re-adjusting the focal length, optimizing the aperture setting, cleaning the lens surface, etc. In a surface detection system, the detection accuracy is improved by checking and solving the imaging fuzzy problem.
Image distortion is another common problem. Possible causes include lens distortion, improper mounting Angle, etc. It should be solved by using a low distortion lens and adjusting the installation Angle. In a three-dimensional measurement system, the measurement accuracy is improved by solving the problem of image distortion.
Signal interference is an important factor affecting imaging quality. Possible causes include electromagnetic interference, power supply noise, etc. To solve this problem, use shielded cables and optimize power supply design. In an industrial detection system, the stability and reliability of the system are improved by solving the problem of signal interference.
Five, maintenance and maintenance skills
Regular cleaning is an important measure to maintain industrial lenses. Special cleaning tools and cleaners should be used, and hard objects or corrosive cleaners should be avoided. In a high precision inspection system, the service life of the lens is extended by regularly cleaning the lens surface.
Environmental monitoring is the key to ensure the stable operation of industrial lenses. You need to periodically check the temperature, humidity, and vibration of the installation environment to ensure that the environment meets requirements. In a semiconductor inspection project, the image quality problem caused by environmental changes is avoided by real-time monitoring of environmental conditions.
Regular calibration is an important measure to maintain the performance of industrial lenses. It is necessary to calibrate focal length, aperture and other parameters regularly according to the use frequency and application requirements. In a precision measurement system, the measurement accuracy and stability are ensured by regular calibration.
The installation and commissioning of industrial lenses is a systematic project, which requires a comprehensive consideration of all aspects from the preparation before installation to the optimization of debugging, from the troubleshooting of common problems to the maintenance skills. Through the correct installation and commissioning, not only can give full play to the performance of the industrial lens, but also extend its service life, improve the stability and reliability of the system. With the continuous progress of technology, the installation and debugging skills of industrial lenses will also be continuously optimized to provide more powerful visual perception for intelligent manufacturing. In the future, the deep integration of industrial lenses with new technologies such as artificial intelligence and 5G will open a new chapter in
machine vision Lenses.